Digital Twins through Extended Reality
We are currently immersed in a new industrial revolution. The first revolutions were brought about by the railroad and the steam engine, the fourth (and fifth) industrial revolution comes with the digitization and automation of industrial plants.
One of the essential elements in this process is the Digital CufflinksThe software is capable of simulating and analyzing industrial processes, allowing digital copies of all elements, processes, production lines, machinery... everything to be more efficient, have more control and be able to make more accurate decisions.
What are Digital Twins?
The Digital Twin o digital twin is an exact replica of a product, a service or an industrial plant with the same features or functionalities of the original. This digital copy allows us to interact with it, perform tests, modifications, see results... it allows us to understand and predict the performance characteristics of their physical equivalentwithout taking the risks involved in making these changes in the real world.
The Digital Twin is used throughout the entire product life cycle for simulate, predict and optimize both the product and the production system before investing in prototypes and physical assets.
The Digital Twin goes from the most basic version of replication (a digitized map or a 3D plan) to versions where thousands of intelligent objects interact with the information in real time, making predictions about the behavior of the physical industrial plant.
All this is thanks to the automation and digitization processes of Industry 4.0, to Artificial Intelligence and Big Data in data processing and machine learning and to the Internet of Things (IoT) in the interaction with the machinery.
Also to the Extended Reality (AR/VR) in the visualization of the final Digital Twin thanks to 3D virtual environments (Virtual Reality) and the superimposition of digital elements on the machinery itself (Augmented Reality).
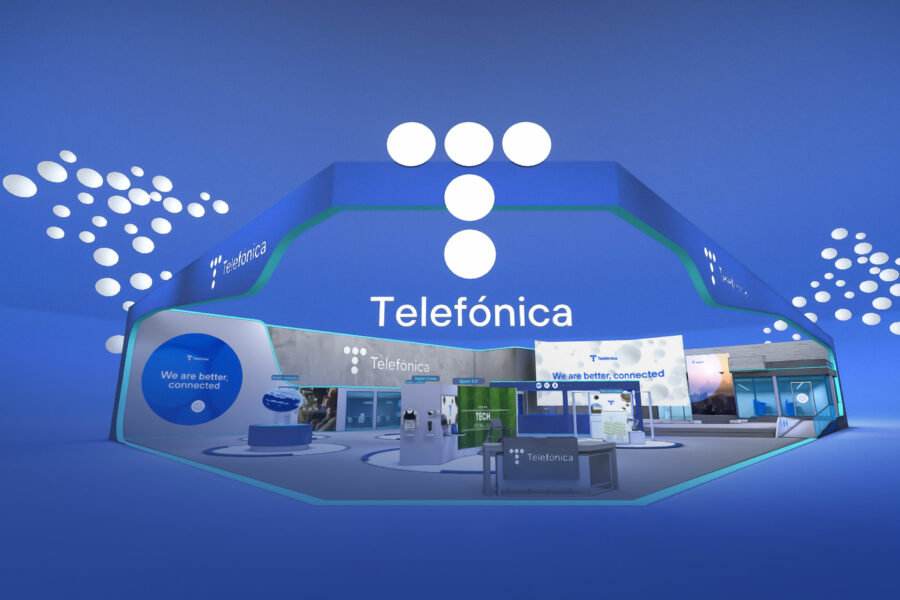
Types and examples of Digital Twins
The digital twin o Digital Twin has multiple applications, especially at the industrial level. In general, there are three types of Digital Twins: production, product and performance.
To these three could be added the Digital Twins, which are focused on training, the Virtual Trainingsand even those focused on the promotion of the industrial company, that is to say, digital twins prepared specifically for display at trade fairs, customers and 3D catalogs.
Digital Production Cufflinks
A Digital Twin applied in the industrial production can help to validate the efficiency of manufacturing processesbefore even starting them up.
In these simulations, the following can be set all parametersThe system is designed for all types of production lines, from heights and travels, to speeds and types of machines to be incorporated into the production line. Allowing all kinds of new ideas and innovations to be tested, ensuring their feasibility before changes are made on the actual production floor.
In addition, once the industrial plant is activated, the placement of sensors makes it possible to real-time performance data collection. Everything to create the most efficient process possible.
The Digital Twin of the plant not only accounts for machinery, but also human teams, supplier delivery times... using all the data from the Digital Twin, companies can avoid equipment downtime and even predict when preventive maintenance tasks will be necessary. This accurate information flow allowsfaster manufacturing operationsmore efficient and more reliable.
Digital Product Cufflinks
Digital Twins go one step beyond 3D prototyping of products or new production lines, with the digital twins not only do these new ideas materialize, but they also become validates your performance virtually with simulations and all kinds of tests.
It enables us to analyze the performance of products under various conditions and to perform adjustments in the virtual world to ensure that your physical version meets all requirements and optimal parameters.
In addition, the Digital Twin product is also a unique promotion and sales toolWe have a wide range of services, both in meetings with clients and product presentations at large events.
Showing the product in different situations, supporting the sales force with your messages and value propositions, as in the Digital Twin of the Telefónica's booth for the Mobile World Congresswhere, in addition to virtualizing the new products presented at the fair, a digital replica of the stand itself was also developed.
Digital Performance Cufflinks
Machinery, IoT products (with Internet of Things technology) and smart industrial plants generate a massive amount of data about their utilization and efficiency; the digital twins focused on performance seek to capture all of this data for their analysis and subsequent use in decision making.
With this data and Digital Twins, companies can obtain information for efficiency improvements in the production systemThe company's business model is based on the use of the latest technology, the capture and analysis of operational data, and even the generation of new business opportunities.
Digital Training Cufflinks
To the first three types of Digital Cufflinks we can add one more, the Digital Twin dedicated to the training of professionals. Where thanks to new immersive technologies (AR/VR), these Digital Twins give the possibility to train autonomously in complex and/or dangerous tasks through controlled 3D simulations.
All this is done before performing them in a real situation and without the need to allocate extra resources such as trainers or the machinery itself for this purpose.
This is a real challenge for the revolution in the industrial sectorThe company can save time and money, train more workers and, above all, ensure that everyone receives the same accurate and quality training, as it is not altered by external factors.
Among the solutions already developed in this area are the entire Virtual Training line. Customized training in Virtual Reality companies in different industrial sectors such as the professional training of workers in the manufacturing industry and the Global Spedition o the training of healthcare professionals in the preparation of the latest liquid medicine of Boehringer Ingelheim.
In addition to Virtual Trainings, examples of Digital Twins that have already been implemented include initiatives such as the one developed in the city of Singapore. Virtual Singapore is a digital twinThe city is an exact copy of the Malaysian city in which tests and analyses can be carried out to see what impact some urban policies would have before they are implemented.
At the European level, we find the Destination Earth (DestinE)an ambitious digital twin of planet Earth that aims to be able to predict how the climate will evolve, when weather events will occur and the impact that human actions such as deforestation will have on the planet. The project is still in the development phase and the Digital Twin is expected to be completed by 2030.
The big role of Digital Twins thanks to Extended Reality
The incorporation of the Digital Twins into the industrial world is revolutionizing data collectionThe simulation of possible situations and the flexibility and continuous adaptation of the production lines.
However, this large real-time database was missing one last key element to make the data available in real time. digital twins the great revelation of Industry 4.0, its visual representation. Accessibility, naturalness and interaction between the machine and the operators, between data and human beings, is the great contribution offered by the incorporation of Extended Reality to the equation.
But, ¿what is Extended Reality? This is the term that encompasses the immersive technologies of the Augmented Reality, Virtual Reality and Mixed RealityThe "immersive realities" concept, referring to all the innovative solutions that combine the characteristics of these immersive realities.
From immersing users in virtual environments The new technologies can be used to create a completely digital world (Virtual Reality), to superimpose 3D digital elements on the real world (Augmented Reality), and to generate the ultimate interaction between the real and digital worlds (Mixed Reality). Three possibilities that, in Industry 4.0, change forever all the traditional processes and workflows of companies.
You may be interested in→ Differences between Augmented Reality and Virtual Reality
Benefits of Digital Twins in Extended Reality
Putting this technology into practice means an improvement in the efficiency, management, competitiveness and productivity of industrial plants and the most cutting-edge companies in Industry 4.0. And even more so if the Digital Twins materialize through Extended RealityThe technologies such as Virtual Reality (VR) or Augmented Reality (AR) help to visualize all the data and to approach all the information in a humanized and gamified way. Thus, Digital Twins are implemented in our day-to-day life with the following benefits for companies:
- New human-machine communication channel. Digital Twins based on the immersive technologies of Extended Reality represent a new way of communication and interaction between machines and people. Going from simply operating the machine to being able to communicate with it accurately and in real time. Whether through VR glasses or Augmented Reality devices, workers will be able to access information, tutorials, notifications, videos and even remotely manage several machines at the same time.
- Predictive maintenance. Virtual Twins allow to know in real time the status of a machine or industrial plant and to perform exhaustive and accurate analysis of all possible parameters and situations that may affect them. In addition, it allows to predict possible incidents, saving time and money in decision making.
- Access to real-time information. Digital Twins supported by Extended Reality allow access to sensor and machine status information remotely and remotely controlled through a Virtual Reality simulator or through the mobile device itself in situ, by superimposing 3D elements on top of it with Augmented Reality.
- Boosting the human team. The digital twins are a great support for professionals, as they are a great help for plant operators to know, just by looking at a machine, if it needs maintenance, thanks to real-time data and a guided system of its use or operation.
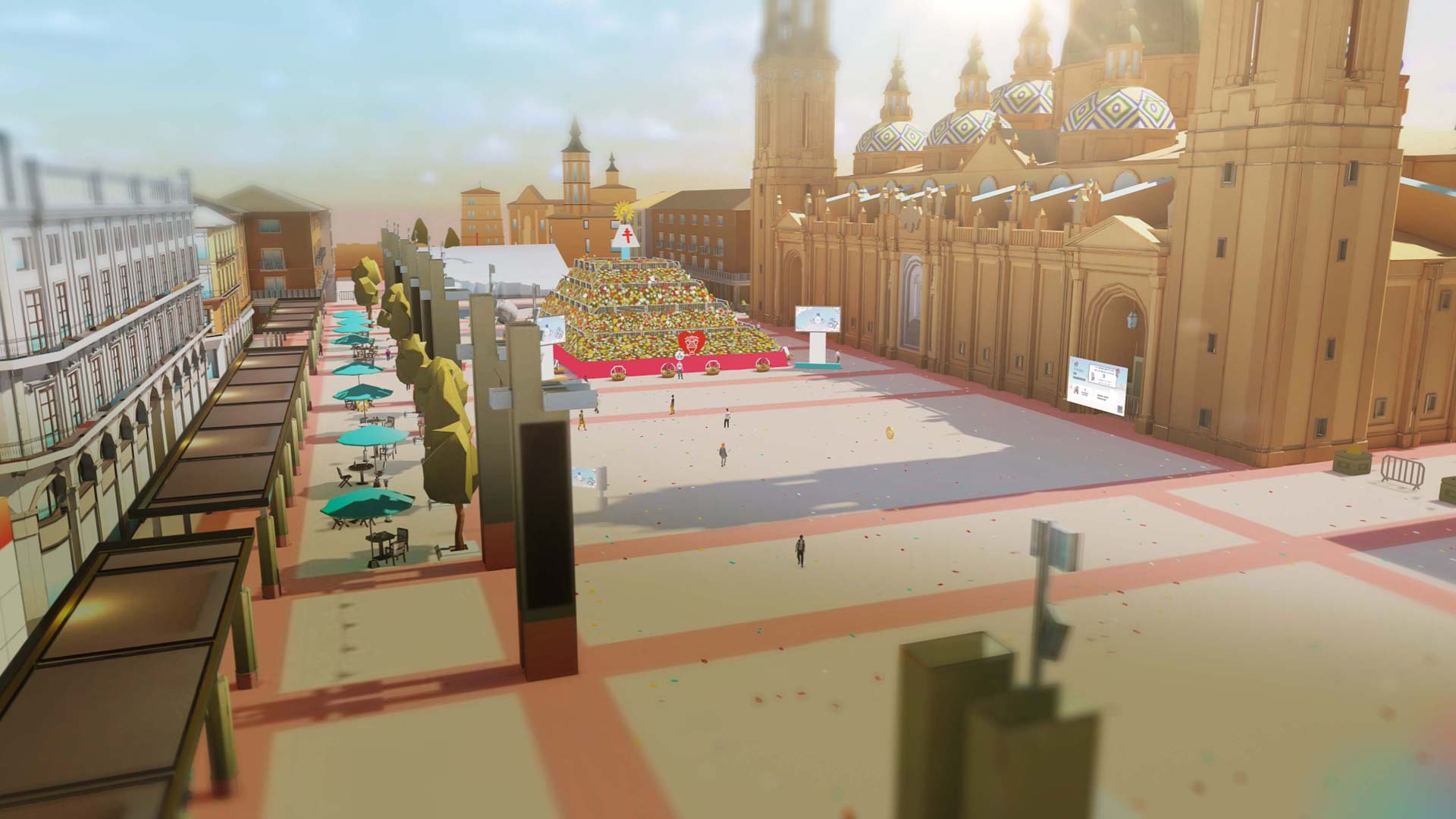
The future of Digital Twins
The future of the industry is Digital Twins, of this there is no doubt. But what is the future of this technology? It is expected that the Digital Twins will continue to work and innovate on the human-machine interactionto make it much more natural and real.
In addition, with the definitive incorporation of the Artificial Intelligence in companies and the latest 3D rendering and development systems, it is only a matter of time before more organizations incorporate Digital Twins into their production lines. Why? The technology will be much more accessible and the time and effort to digitize and virtualize industrial plants will be much less.
At Imascono we have been working for more than 12 years with industrial companies of all fields and sizes. Being part of their digital metamorphosis strategy with the implementation of their Digital Twins. Our goal is to help companies to overcome barriers and take full advantage of the benefits of Extended Reality and Digital Twins in its operations and industrial processes.
Our engineers and designers will be happy to answer all of your questions and discuss how we can adapt our Digital Twin solutions to your company's specific needs.Contact with us and we will help you make the leap to the next level of Industry 4.0!